Aluminium and the metalwork of Jiro Nagase
At 31 years of age, Jiro Nagase is still in the early stages of pursuing his craft. Based in Tokyo’s Kita Ward, the emerging metal craftsman has been developing an impressive collection of products and artworks in recent years. Hand-hammered bowls, free-standing lights and modular furniture are among his works, which can be found in a growing number of shops and galleries around the country. For the past three years, Nagase has been focusing on aluminium, exploring the material’s potential in the world of craft.
As common as aluminium may be in our everyday lives, appearing everywhere from architecture to aircraft components and kitchen utensils, the material has a relatively short history. As extraction technology developed in the 19th century, around the time of the Industrial Revolution, the metal’s use expanded as its properties and abundance proved a perfect match for industrial manufacturing. “Compared to steel and copper, aluminium has a short history of use as a craft material, so I think there’s still a lot to be learnt about its use and presentation. It’s not just a case of applying techniques developed for steel and copper; aluminium’s unique potential is yet to be fully explored,” says Nagase.
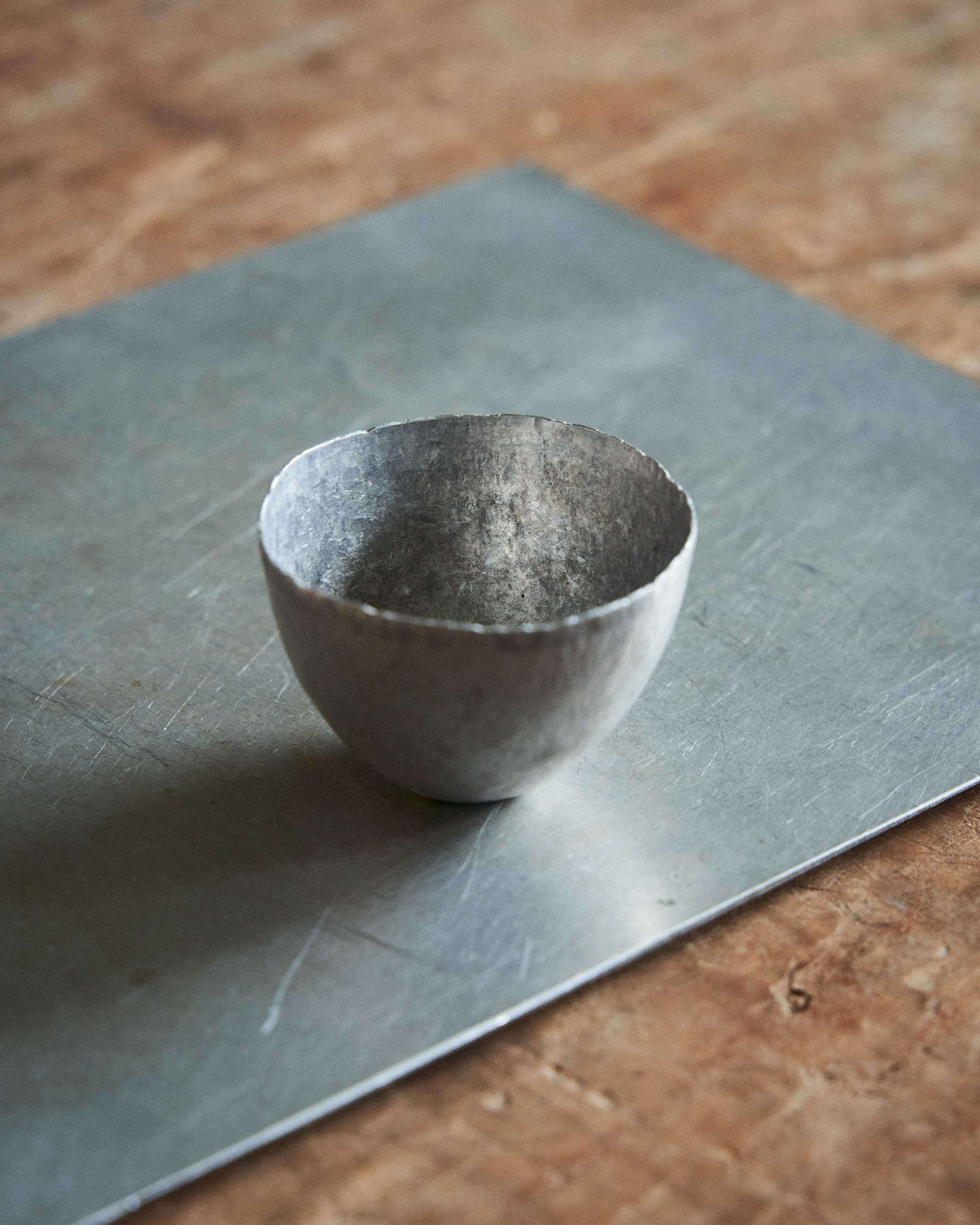
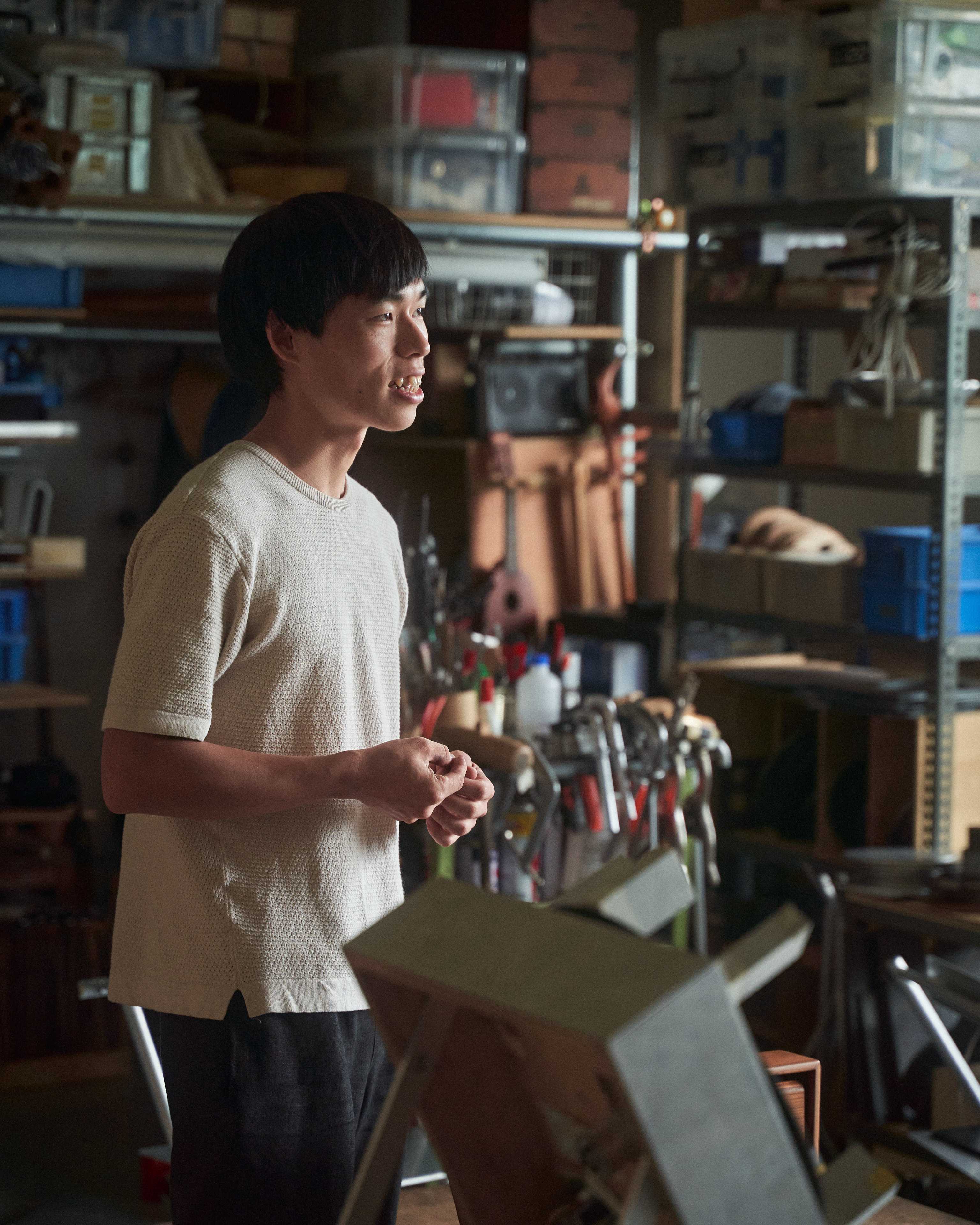
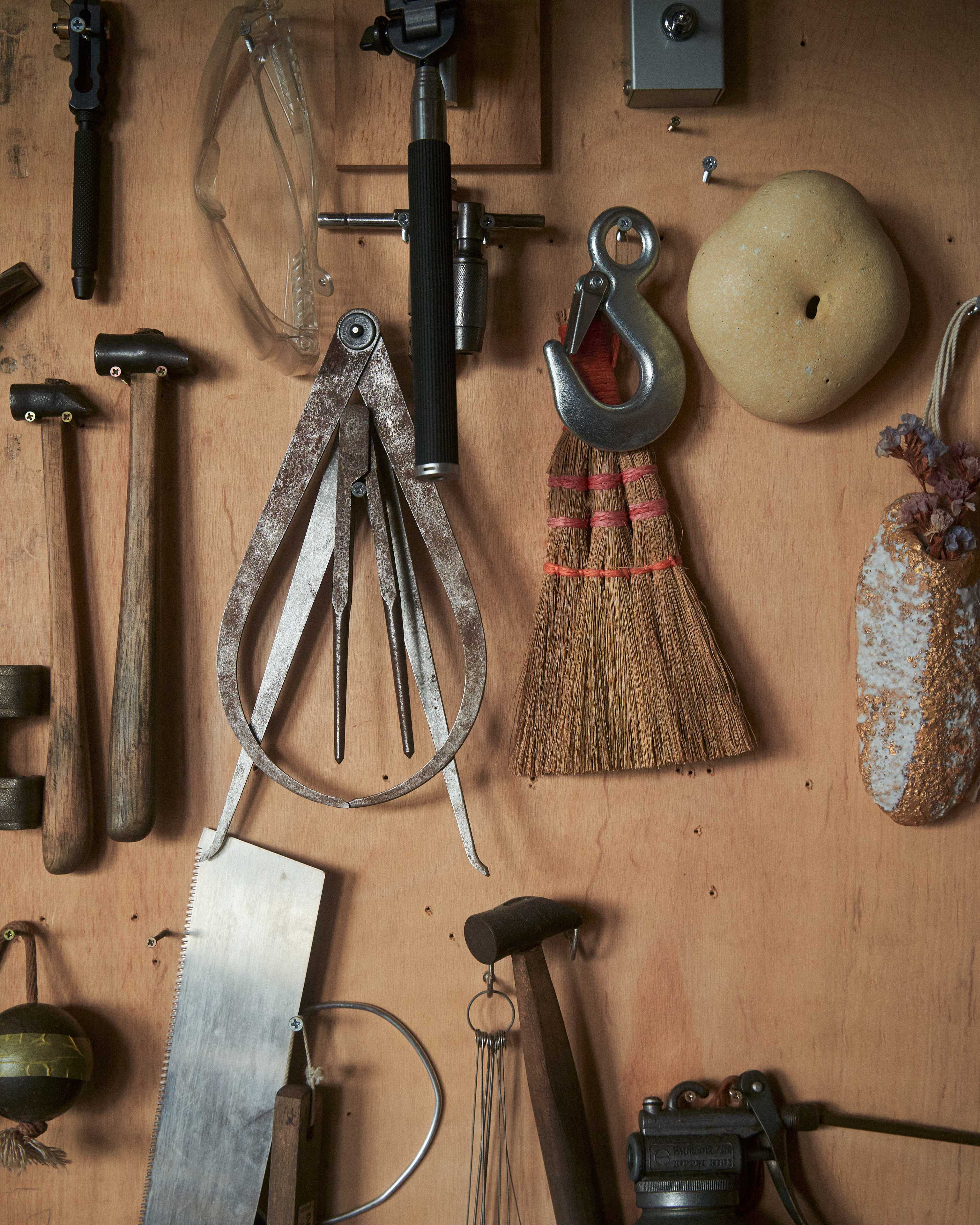
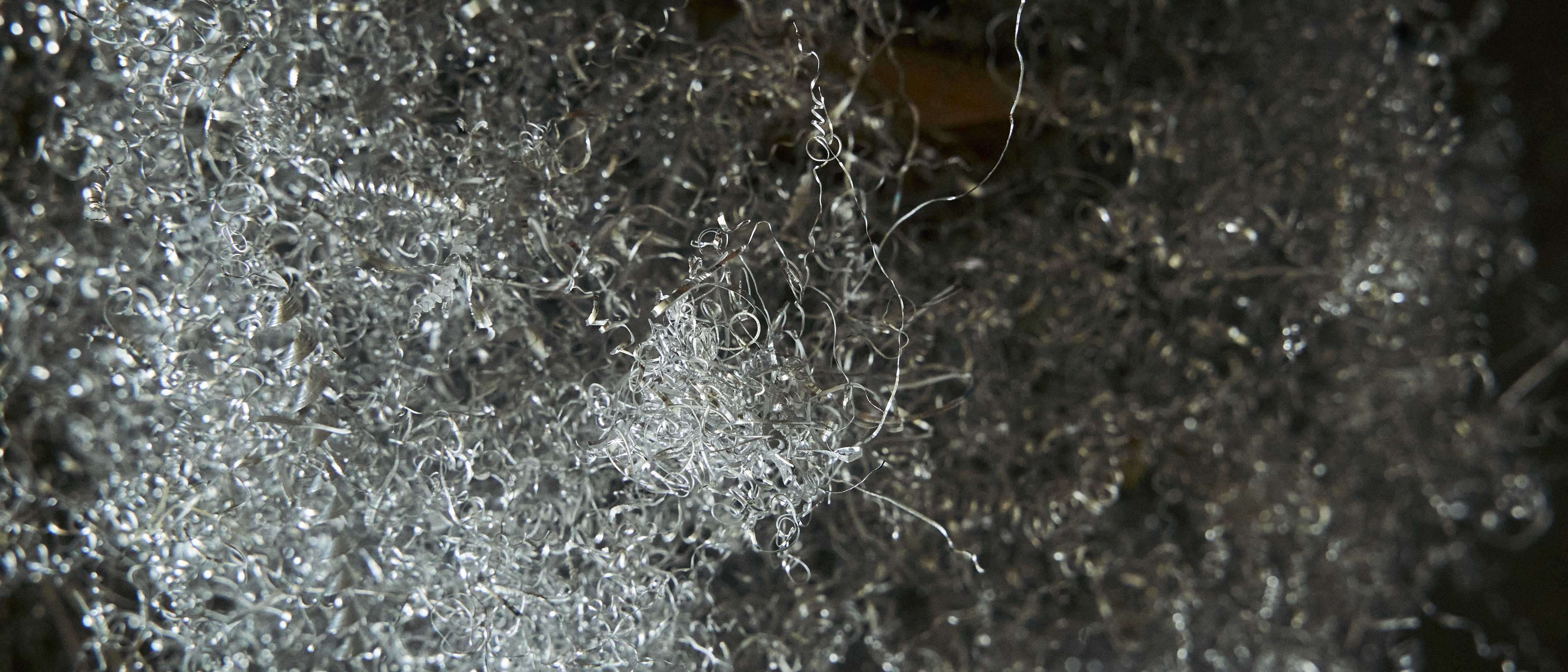
This spirit of enquiry can be felt at Nagase’s workshop in Kita Ward. Seeing his works for the first time, the flat grey texture of the aluminium elements has a calming effect, merging seamlessly into their surroundings. “When a work is completed, the colour and finish of the aluminium shines through. During the production process, I’m conscious of how the material will change through use, but rather than adding a certain character, I aim to make the finish as neutral as possible,” explains Nagase. “The finished state is interesting, but I feel it becomes even more attractive as it ages naturally. I try to create a finish that appeals throughout the transition from new to used. The scratches, marks and stains that tools acquire shouldn’t be seen as a negative, as they add to the allure and our sense of attachment.”
The theme of evolution extends to one of Nagase’s signature products: MFC (Modular Folding Chair). The chair’s design is based on the use of modular parts, providing a platform for various customisations over the duration of its life. Each chair is individually numbered and comes with a hexagonal wrench, making it easy for people to add or adjust parts on their own. “While it’s supposed to serve a function, another interesting thing about this chair is its similarities to a plastic kit model or playing house. It’s an open platform, providing room for you to create and attach your own ideas or style,” says Nagase. In addition to standard options such as backrests and cushions, he has also started experimenting with one-of-a-kind additions including cup holders and clamps.
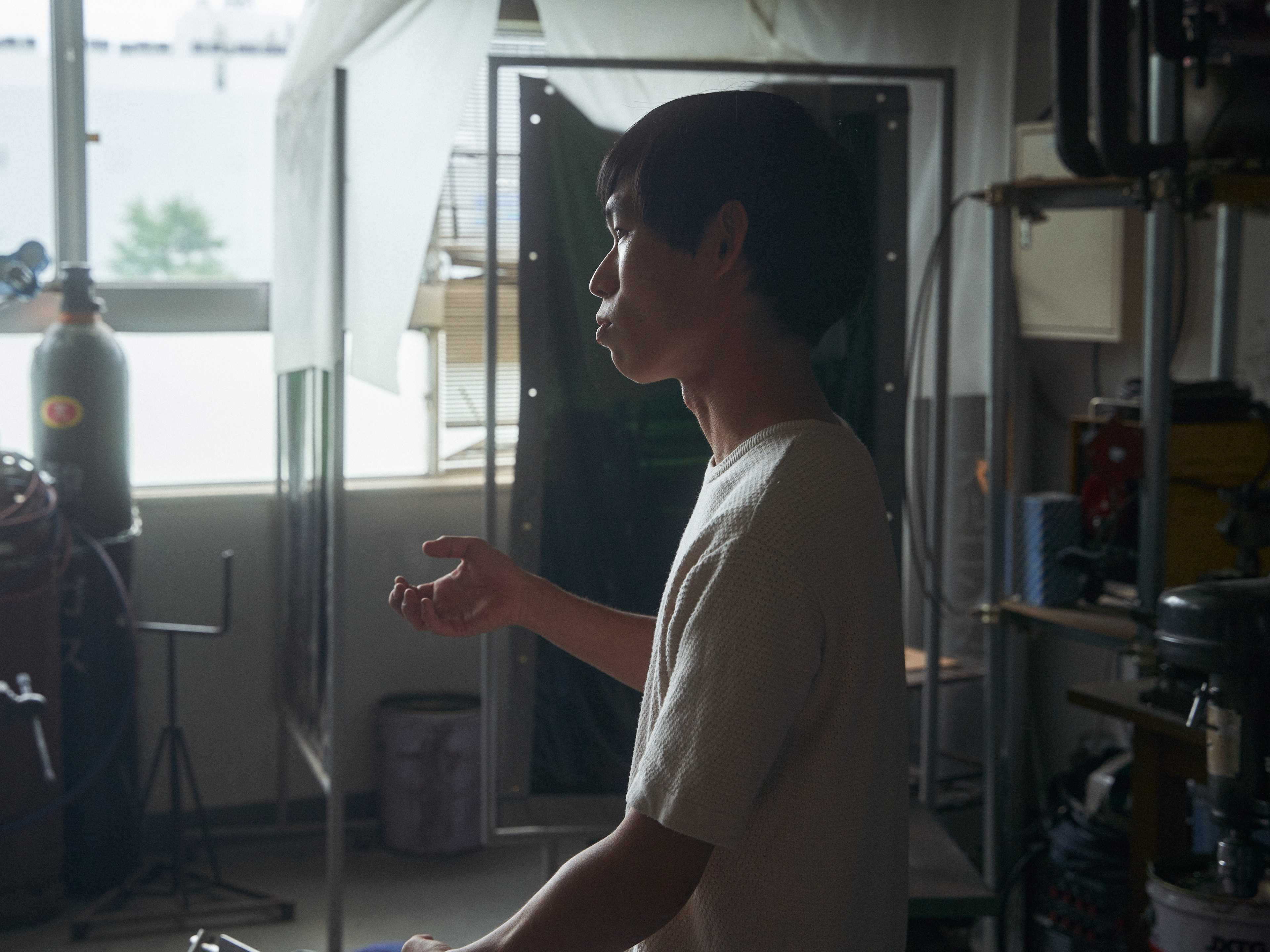
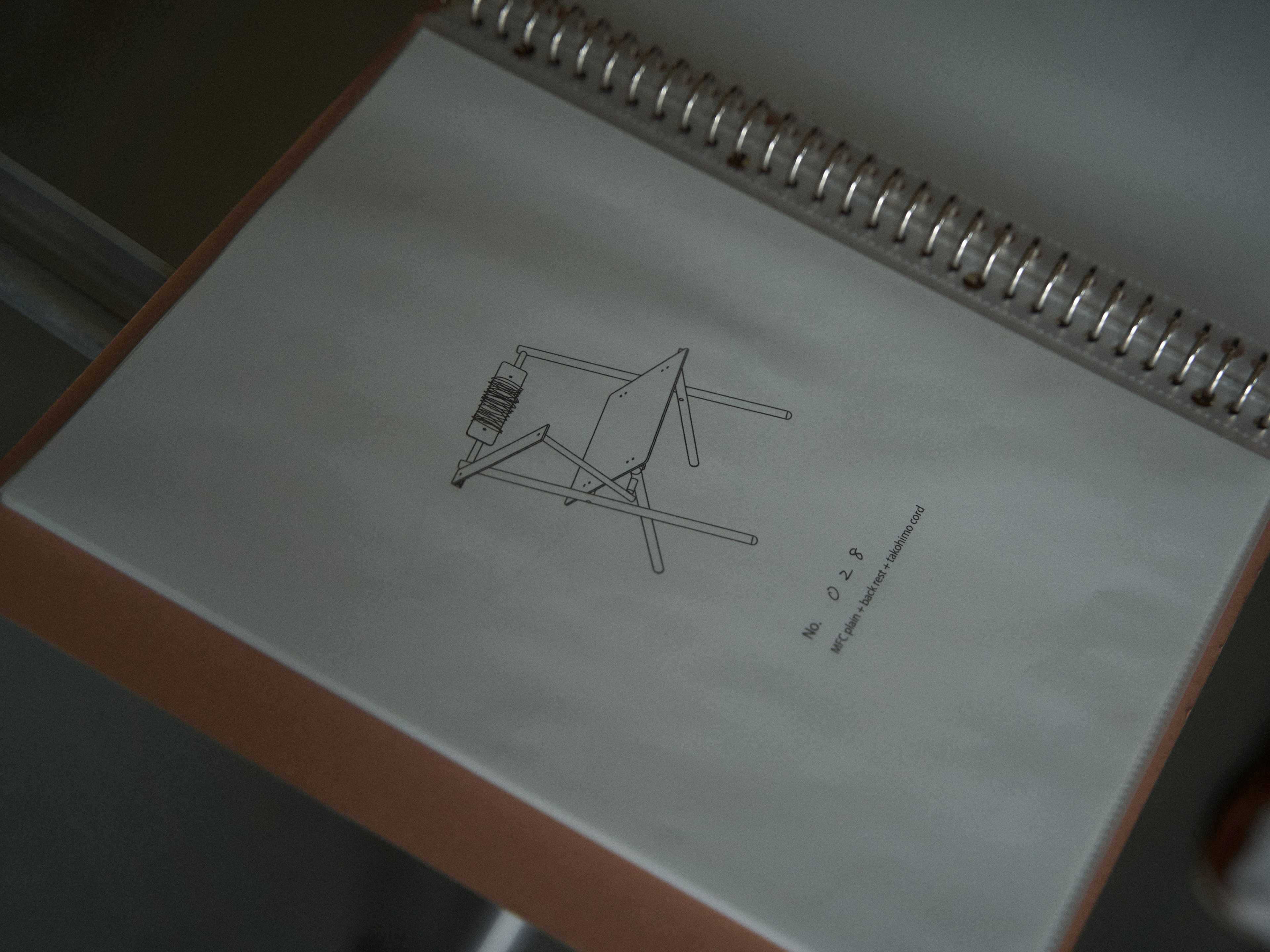
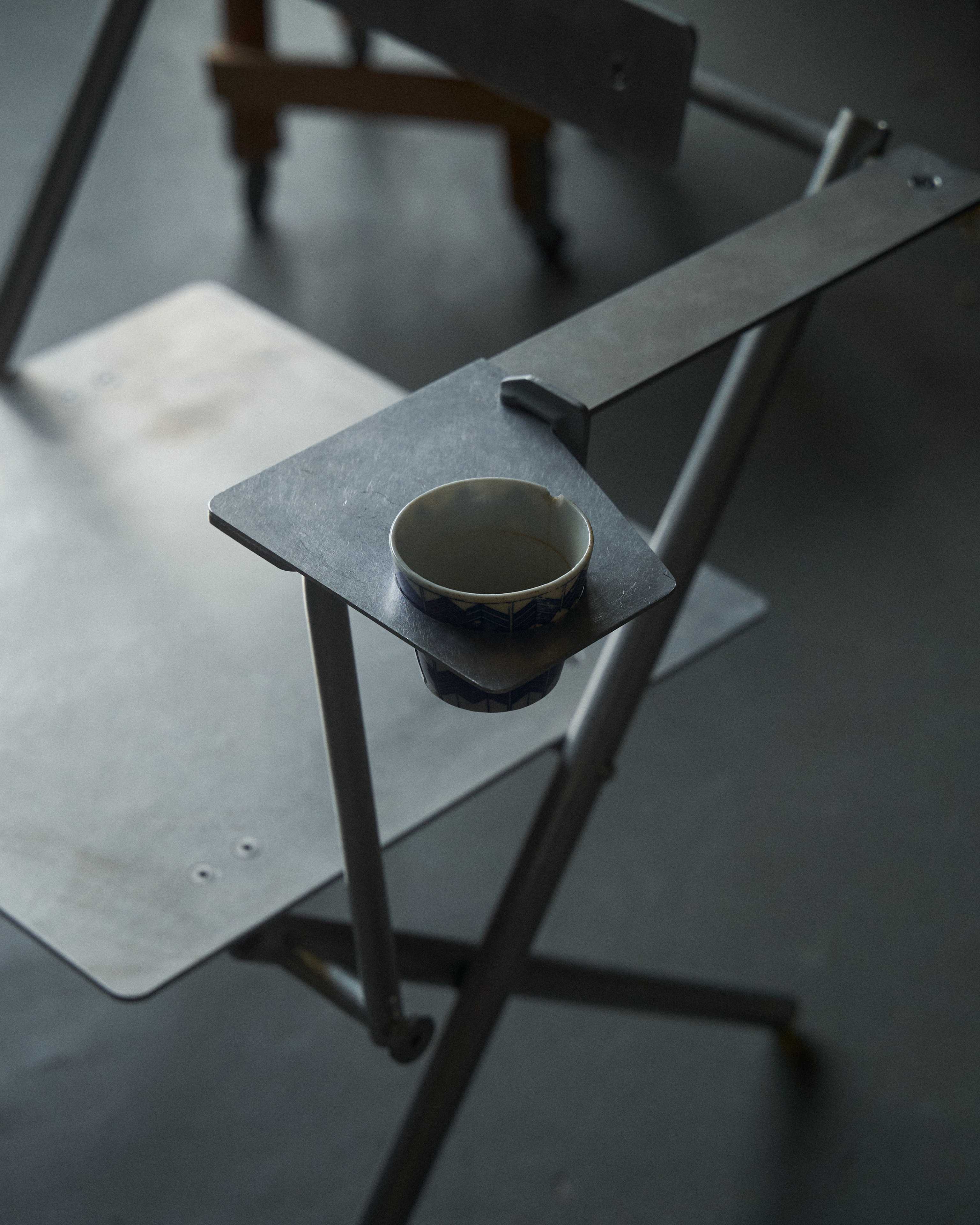
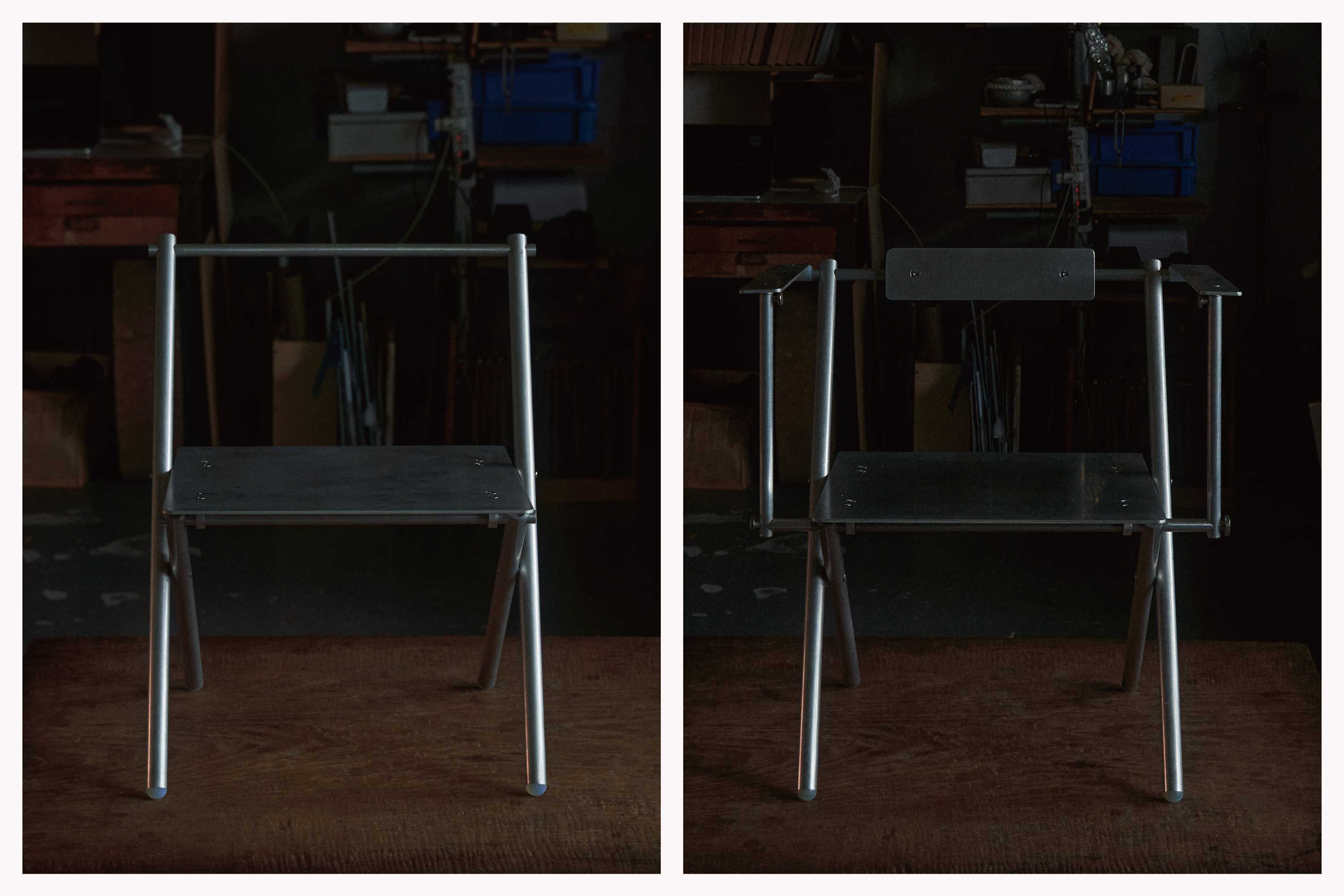
Other products draw character from the processes applied to the aluminium material. For example, the Caldera series of tableware features unique forms and textures, created by heating, softening and allowing sections to sink into a mould. Another ongoing series features pairs of robust bookends, shaped with a mechanical bandsaw. The blade cuts a wavering line through a solid block of metal, creating harmonious forms with a rugged profile.
“The bookends aren’t industrial products, as they are unique and made by hand, but at the same time, the surface created by the bandsaw would be considered unfinished from a craft perspective. This approach to making seems similar to the world of forging. During the Meiji era, when craftspeople made shiny bowls and craft wares through forging, they strived for a level of craftsmanship that appeared beyond the limits of human possibility. However, as technology developed, machines eventually exceeded their skills, which I believe contributed to a rise in people creating works with evidence of their handiwork.”
As the fields of manufacturing and craft have continued to develop, one of Nagase’s aims is to capture the tools and techniques of his craft as it stands today. “Even in small workshops, machines like the bandsaw are being replaced by laser cutters. In the future, high-precision machines may be all that remain, which will remove the need for manual processes. In 20 or 30 years’ time, I think it will be interesting to look back at the works I’ve created with these machines.”
Listening to the stories behind Nagase’s various works, each one starts to feel like an experiment, an investigation into an idea, process or problem that needs solving. As his journey continues, the craftsman shows that within a single material lies a world of possibilities.
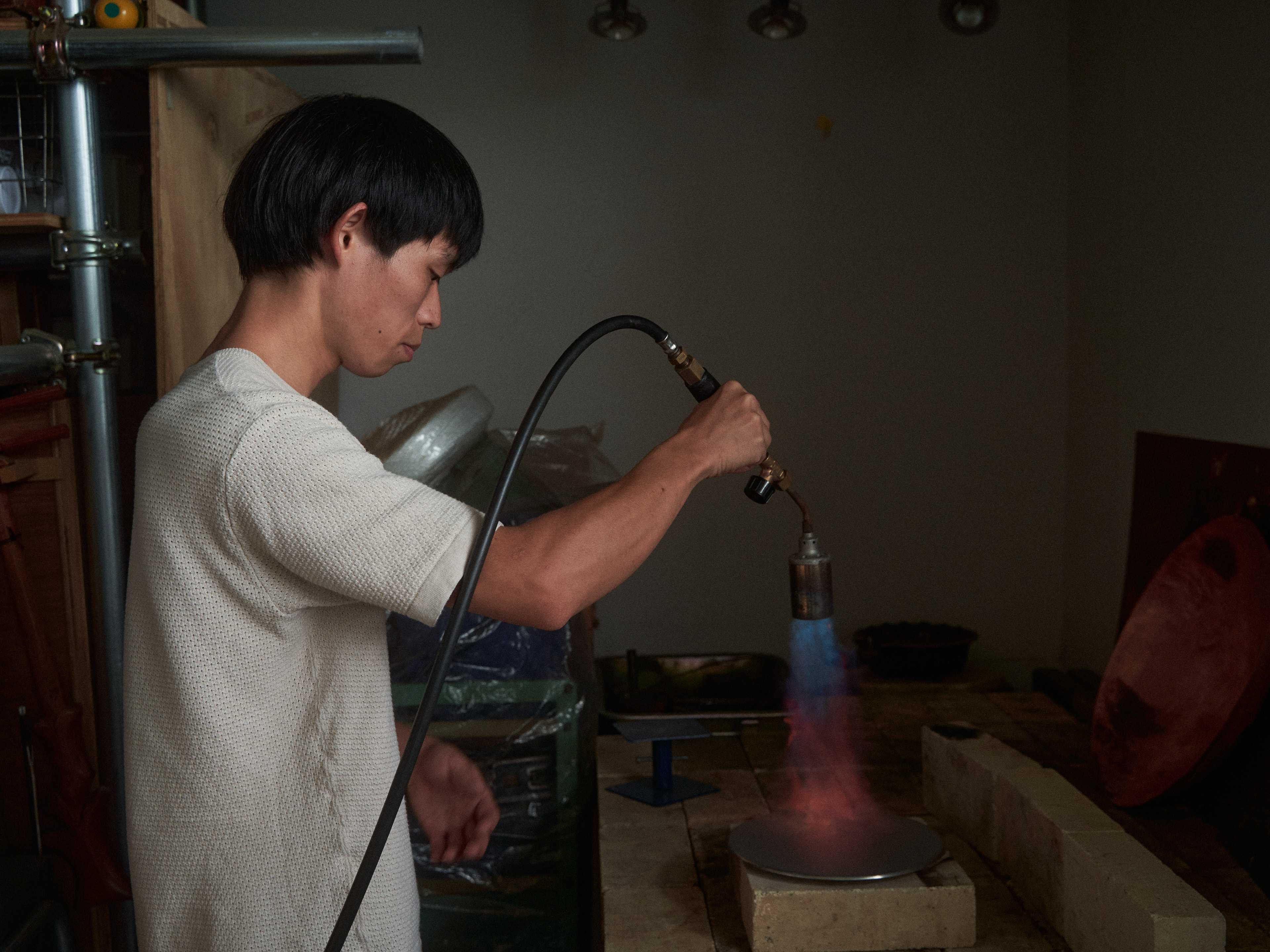
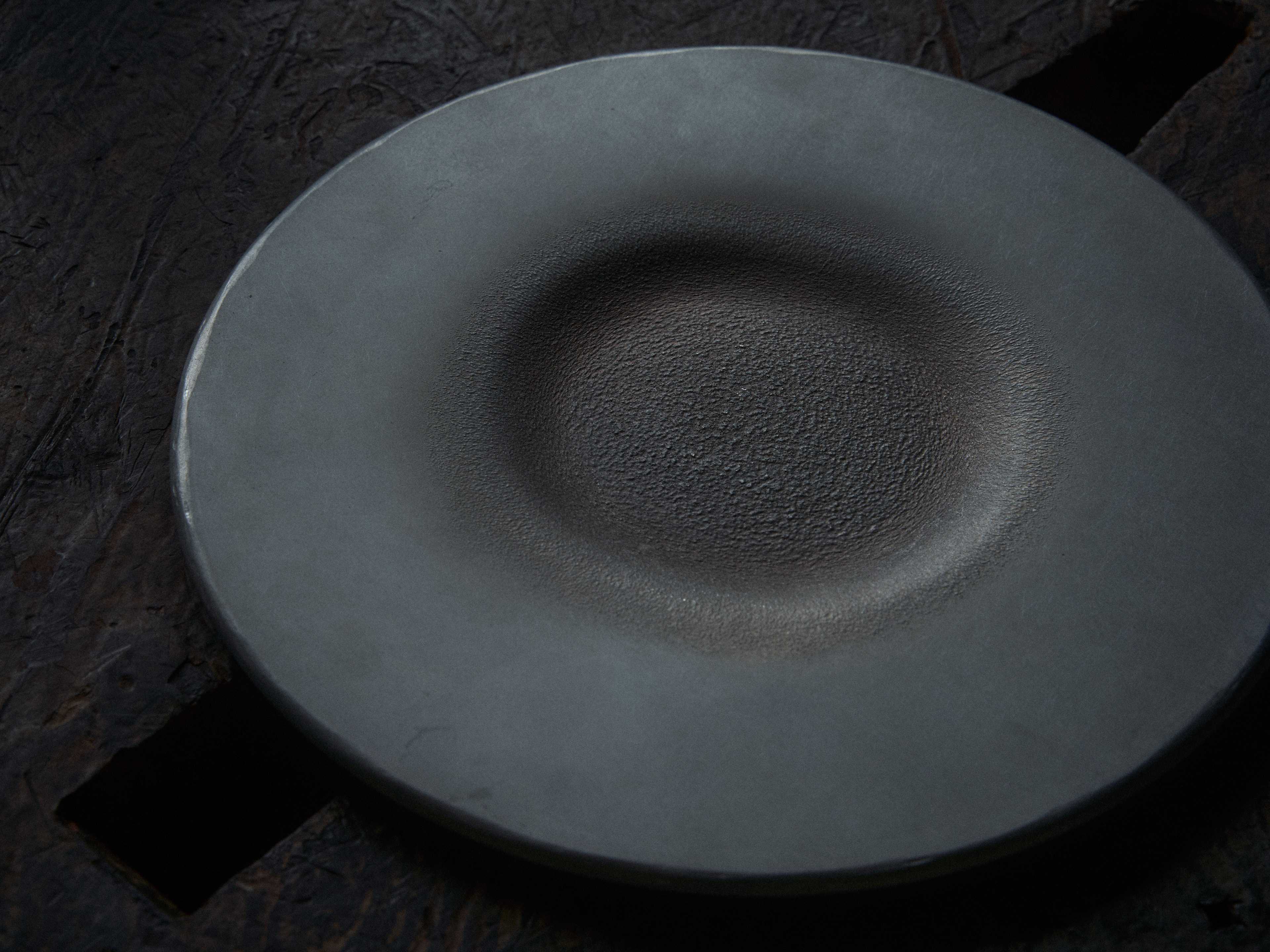
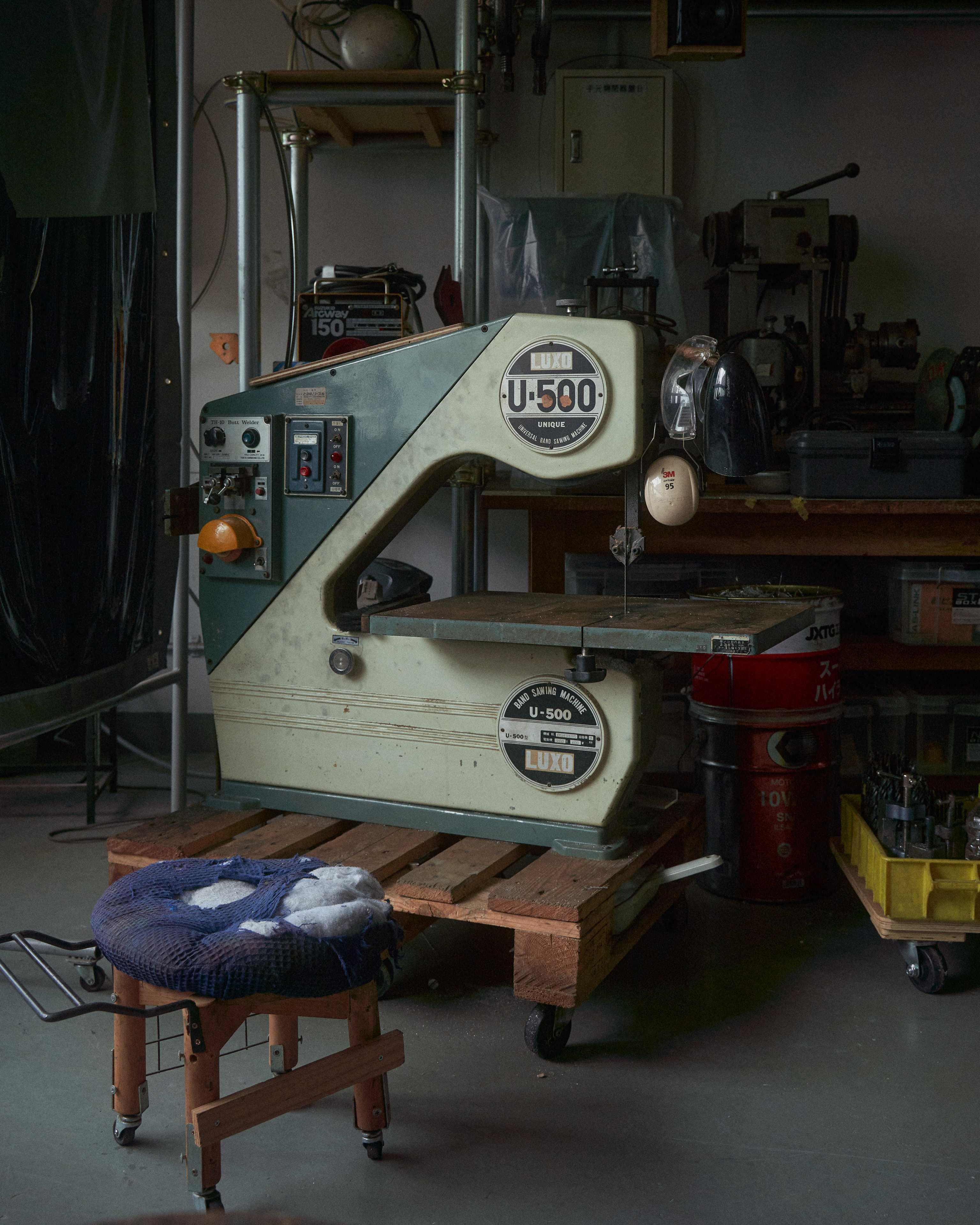
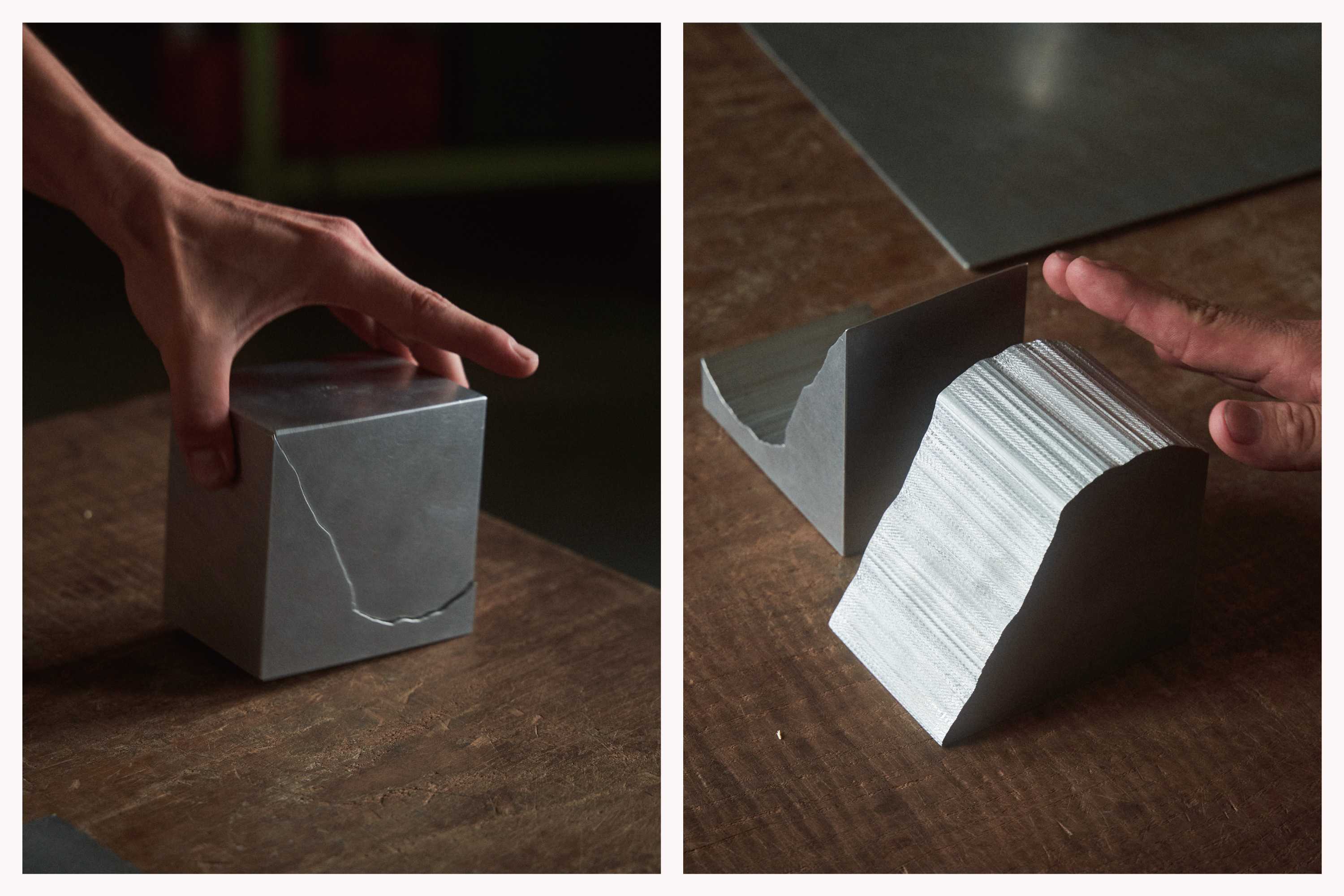
Text by Ben Davis
Photo by Daisuke Hashihara